COMBINES ATTRACTIVE APPEARANCE WITH EXCELLENT MECHANICAL PROPERTIES.
PC1142 |
PENNY VEIN METALLIC |
CHEMISTRY |
POLYESTER TGIC B |
REGULAR CURE TEMP |
375F / 15 MIN |
MIN TEMP |
350F / 20 MIN |
MAX TEMP |
400F / 10 MIN |
RECOMMENDED THICKNESS |
2.0-3.0 mils |
PENCIL HARDNESS |
H minimum |
SPECIFIC GRAVITY |
1.40 +/-0.05 g/cm³ |
THEORETICAL COVERAGE |
137 sq.ft/lb/mil |
PENCIL HARDNESS |
2H minimum |
GLOSS LEVEL (60°) |
NA |
SALT SPRAY |
500 hours |
BALL IMPACT |
40 in/lb |
SDS Sheet info # |
#6B – Polyester TGIC (Group B) |
SDS link |
https://emeraldcoatings.com/sds-sheets/ |
*Clear Coat Recommended, will Improved Mar Resistance and will improve the over all look and depth of the metallic finish. *When coating in 2-3 stages, always particularly cure the base coat around 50-75% of the recommended cure schedule to allow the top coat to properly cross-link with the base coat. This method of curing will result in the best possible bond between coats. Over curing the base coat can cause possible delamination between coatings. |
ROCKSTAR BLACK TGIC POLYESTER POWDER
HAS A MIXTURE OF MEDIUM TO LARGE GOLD FLAKE THROUGH THE FINISH. GET THE MOST BLING FOR YOUR BUCK
CHEMISTRY |
ROCKSTAR BLACK |
CHEMISTRY |
Polyester TGIC Metallic |
REGULAR CURE TEMP |
375F 13-20 MIN |
MIN TEMP |
356F 15-25 MIN |
MAX TEMP |
400F 10-15 MIN |
RECOMMENDED THICKNESS |
1.5 TO 3.5 MILS |
PENCIL HARDNESS |
2H |
SPECIFIC GRAVITY |
1.26 +/- .05 |
THEORETICAL COVERAGE |
56 sq/ft @ 2.0 mils |
PENCIL HARDNESS |
2H minimum |
GLOSS LEVEL (60°) |
85-95+ |
SALT SPRAY |
1,000 hours |
BALL IMPACT |
80 in/lb |
SDS Sheet info # |
#9 – Polyester TGIC Metallic |
SDS link |
https://emeraldcoatings.com/sds-sheets/ |
*Clear Coat Recommended, will Improved Mar Resistance and will improve the over all look and depth of the metallic finish. *When coating in 2-3 stages, always particularly cure the base coat around 50-75% of the recommended cure schedule to allow the top coat to properly cross-link with the base coat. This method of curing will result in the best possible bond between coats. Over curing the base coat can cause possible delamination between coatings. |
Great to use as a base coat for candy colours.
PC1177 |
SILVER VEIN METALLIC |
CHEMISTRY |
POLYESTER TGIC C |
REGULAR CURE TEMP |
15 Minutes@ 375°F |
MIN TEMP |
NA |
MAX TEMP |
NA |
RECOMMENDED THICKNESS |
2.5 TO 3.5 MILS |
PENCIL HARDNESS |
2H |
SPECIFIC GRAVITY |
1.68 +/- .05 |
THEORETICAL COVERAGE |
56 sq/ft @ 2.0 mils |
PENCIL HARDNESS |
2H minimum |
GLOSS LEVEL (60°) |
NA |
SALT SPRAY |
1,000 hours |
BALL IMPACT |
80 in/lb |
SDS Sheet info # |
#6C – Polyester TGIC (Group C) |
SDS link |
https://emeraldcoatings.com/sds-sheets/ |
*Clear Coat Recommended, will Improved Mar Resistance and will improve the over all look and depth of the metallic finish. *When coating in 2-3 stages, always particularly cure the base coat around 50-75% of the recommended cure schedule to allow the top coat to properly cross-link with the base coat. This method of curing will result in the best possible bond between coats. Over curing the base coat can cause possible delamination between coatings. |
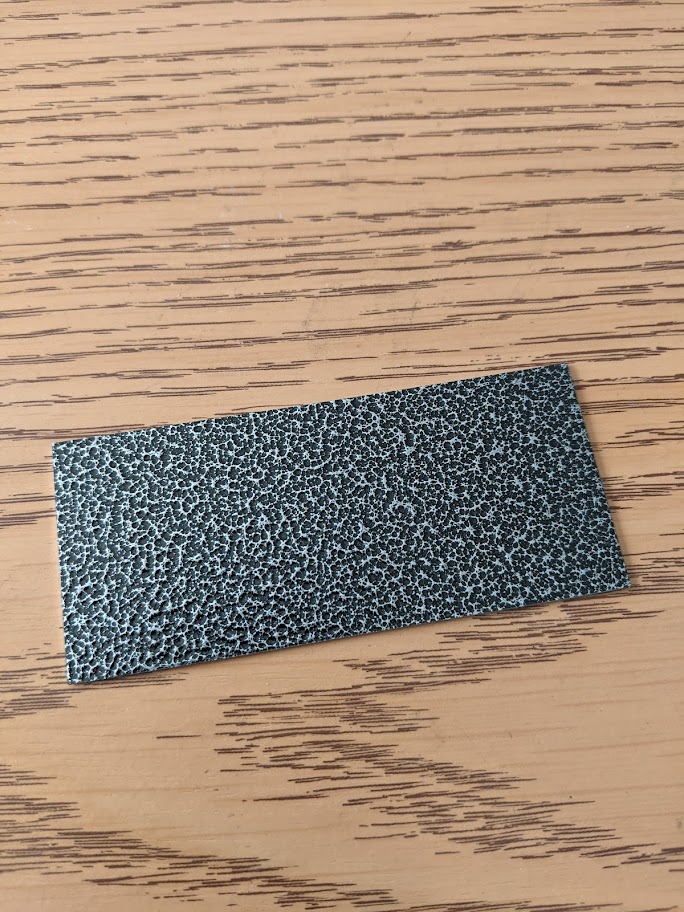
SAFETY YELLOW has been updated to the new TGIC free version. Do not mix with older versions.
PC1167 |
SAFETY YELLOW (TGIC FREE VERSION) |
CHEMISTRY |
POLYESTER TGIC-FREE |
REGULAR CURE TEMP |
356F 10-23 MIN |
MIN TEMP |
320F 15-30 MIN |
MAX TEMP |
400F 5-15 MIN |
RECOMMENDED THICKNESS |
2.5-3.5 mils |
PENCIL HARDNESS |
2H minimum |
SPECIFIC GRAVITY |
1.2-1.8 g/cm3 |
THEORETICAL COVERAGE |
51.5 ft2 /lb at 2.5 mils |
PENCIL HARDNESS |
2H minimum |
GLOSS LEVEL (60°) |
80-95+ |
SALT SPRAY |
1,000 hours |
BALL IMPACT |
80 in/lb |
SDS Sheet info # |
#4 – Polyester TGIC Free |
SDS link |
https://emeraldcoatings.com/sds-sheets/ |
ZINC RICH PRIMER EPOXY
KNOWN FOR OUTSTANDING CORROSION RESISTANCE FOR STEEL PARTS ONLY
PC1206 |
ZINC RICH PRIMER |
CHEMISTRY |
Epoxy |
REGULAR CURE TEMP |
10 Minutes@ 350°F |
MIN TEMP |
NA |
MAX TEMP |
NA |
RECOMMENDED THICKNESS |
1.5 TO 2.5 MILS |
PENCIL HARDNESS |
2H |
SPECIFIC GRAVITY |
2.95 +/- .05 |
THEORETICAL COVERAGE |
NA |
PENCIL HARDNESS |
2H minimum |
GLOSS LEVEL (60°) |
60-85 |
SALT SPRAY |
1,000 hours |
BALL IMPACT |
80 in/lb |
SDS Sheet info # |
#1 – Zinc Primer |
SDS link |
https://emeraldcoatings.com/sds-sheets/ |
ZINC RICH PRIMER EPOXY
KNOWN FOR OUTSTANDING CORROSION RESISTANCE FOR STEEL PARTS ONLY,*When coating in 2-3 stages, always particularly cure the base coat around 50-75% of the recommended cure schedule to allow the top coat to properly cross-link with the base coat. This method of curing will result in the best possible bond between coats. Over curing the base coat can cause possible delamination between coatings. |
Neon Yellow powder coat. The brightest yellow powder coat that we sell. The powder lays down super smooth and flows out to a high gloss finish. LIMITED UV STABILITY
PC1182 |
NEON YELLOW |
CHEMISTRY |
POLYESTER TGIC |
REGULAR CURE TEMP |
375F 13-20 MIN |
MIN TEMP |
356F 15-25 MIN |
MAX TEMP |
400F 10-15 MIN |
RECOMMENDED THICKNESS |
2.5-3.5 mils |
PENCIL HARDNESS |
H minimum |
SPECIFIC GRAVITY |
1.2-1.8 g/cm3 |
THEORETICAL COVERAGE |
51.5 ft2 /lb at 2.5 mils |
PENCIL HARDNESS |
2H minimum |
GLOSS LEVEL (60°) |
80-95+ |
SALT SPRAY |
500 hours |
BALL IMPACT |
20 in/lb |
SDS Sheet info # |
#6A – Polyester TGIC (Group A |
SDS link |
https://emeraldcoatings.com/sds-sheets/ |
LIMITED UV STABILITY. May fade with repeated outdoor exposure, Even with a clear coat you still may see fading *When coating in 2-3 stages, always particularly cure the base coat around 50-75% of the recommended cure schedule to allow the top coat to properly cross-link with the base coat. This method of curing will result in the best possible bond between coats. |
EBONY CHROME
THIS PRODUCT IS ANOTHER ADDITION TO OUR BLACK/SMOKE CHROMES
PC1059 |
EBONY CHROME |
CHEMISTRY |
POLYESTER TGIC A |
REGULAR CURE TEMP |
400F/10 min |
MIN TEMP |
NA |
MAX TEMP |
NA |
RECOMMENDED THICKNESS |
2.0-3.0 mils |
PENCIL HARDNESS |
2-H |
SPECIFIC GRAVITY |
1.24 +/- .05 |
THEORETICAL COVERAGE |
155ft^2 /lb/mil |
PENCIL HARDNESS |
2H minimum |
GLOSS LEVEL (60°) |
85+ |
SALT SPRAY |
1,000 hours |
BALL IMPACT |
160 in/lb |
SDS Sheet info # |
#6A – Polyester TGIC (Group A) |
SDS link |
https://emeraldcoatings.com/sds-sheets/ |
*Clear Coat Recommended, will Improved Mar Resistance and will improve the over all look and depth of the metallic finish. *When coating in 2-3 stages, always particularly cure the base coat around 50-75% of the recommended cure schedule to allow the top coat to properly cross-link with the base coat. This method of curing will result in the best possible bond between coats. Over curing the base coat can cause possible delamination between coatings. |
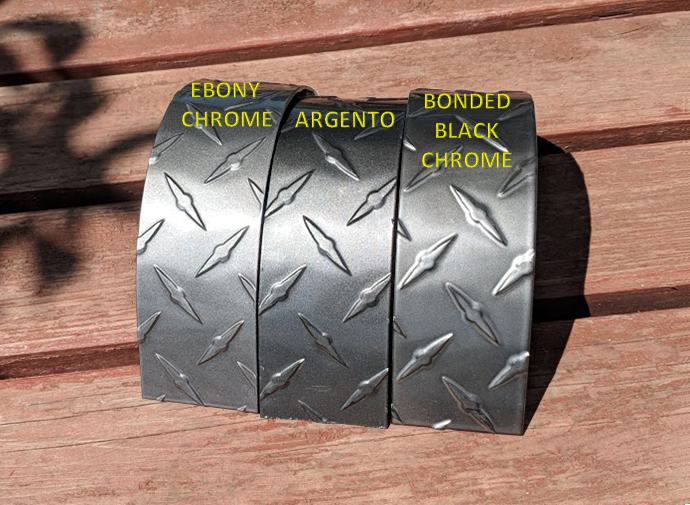
Check out our Wheel Silver for a close match to this colour.
PC1117 |
MIRROR SILVER SPARKLE |
CHEMISTRY |
POLYESTER TGIC A |
REGULAR CURE TEMP |
375F 13-20 MIN |
MIN TEMP |
356F 15-25 MIN |
MAX TEMP |
400F 10-15 MIN |
RECOMMENDED THICKNESS |
2.5-3.5 mils |
PENCIL HARDNESS |
2H minimum |
SPECIFIC GRAVITY |
1.2-1.8 g/cm3 |
THEORETICAL COVERAGE |
51.5 ft2 /lb at 2.5 mils |
PENCIL HARDNESS |
2H minimum |
GLOSS LEVEL (60°) |
80-95+ |
SALT SPRAY |
1,000 hours |
BALL IMPACT |
80 in/lb |
SDS Sheet info # |
#6A – Polyester TGIC (Group A) |
SDS link |
https://emeraldcoatings.com/sds-sheets/ |
*Clear Coat Recommended, will Improved Mar Resistance and will improve the over all look and depth of the metallic finish. *When coating in 2-3 stages, always particularly cure the base coat around 50-75% of the recommended cure schedule to allow the top coat to properly cross-link with the base coat. This method of curing will result in the best possible bond between coats. Over curing the base coat can cause possible delamination between coatings. |
BLACK WRINKLE POLYESTER POWDER
A MUST FOR ANY COATER THAT HAS HARLEY DAVIDSON CUSTOMERS. SPECIALLY FORMULATED TO MATCH S&S MOTORS THIS WEATHER RESISTANT WRINKLE IS PERFECT FOR ACCENTING ANY HARLEY DAVIDSON.
PC1022 |
BLACK WRINKLE |
CHEMISTRY |
Polyester TGIC Free |
REGULAR CURE TEMP |
375F/15 min |
MIN TEMP |
NA |
MAX TEMP |
NA |
RECOMMENDED THICKNESS |
2.2-2.8 Mils |
PENCIL HARDNESS |
HB |
SPECIFIC GRAVITY |
1.31 ± 0.05 |
THEORETICAL COVERAGE |
58.8 SQ. |
PENCIL HARDNESS |
2H minimum |
GLOSS LEVEL (60°) |
30-39% |
SALT SPRAY |
1,000 hrs |
BALL IMPACT |
120 / 40 in/lbs |
SDS Sheet info # |
#7 – Black wrinkle |
SDS link |
https://emeraldcoatings.com/sds-sheets/ |
WEATHER RESISTANT POWDER COATING FOR INTERIOR AND EXTERIOR APPLICATIONS. USE ZINC RICH PRIMER OVER STEEL PARTS FOR EXTERIOR APPLICATIONS |
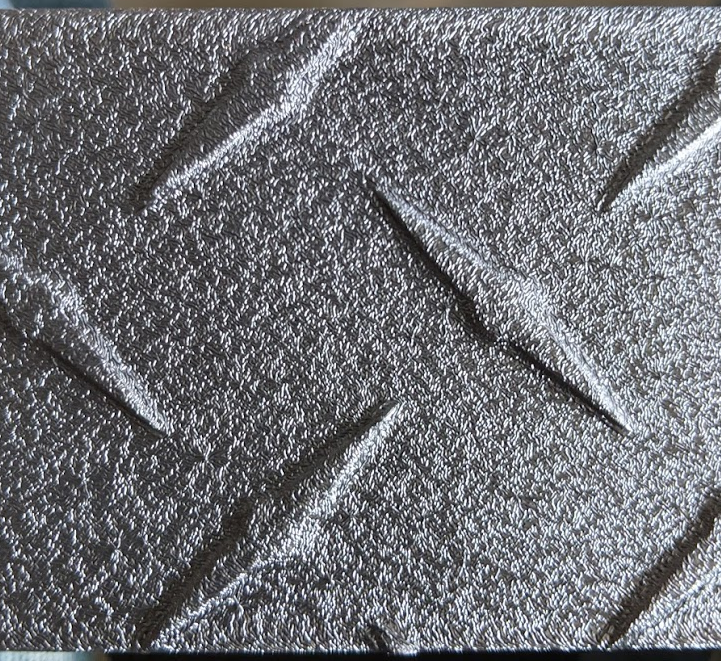
SCREAMIN EAGLE BLACK CRINKLE
PC1173 |
SCREAMIN EAGLE BLACK CRINKLE |
CHEMISTRY |
POLYURETHANE GROUP B |
REGULAR CURE TEMP |
375F/10 MIN |
MIN TEMP |
NA |
MAX TEMP |
NA |
RECOMMENDED THICKNESS |
2.5-4.0 mils |
PENCIL HARDNESS |
H minimum |
SPECIFIC GRAVITY |
1.41 +/-0.05 g/cm³ |
THEORETICAL COVERAGE |
136.38 sq.ft/lb/mil |
PENCIL HARDNESS |
2H minimum |
GLOSS LEVEL (60°) |
0-10 |
SALT SPRAY |
1,000 hours |
BALL IMPACT |
140 in/lb |
SDS Sheet info # |
#5B – Polyurethanes (Group B) |
SDS link |
https://emeraldcoatings.com/sds-sheets/ |
WEATHER RESISTANT POWDER COATING FOR INTERIOR AND EXTERIOR APPLICATIONS, clear coat is not needed but will add extra protection. When coating in 2-3 stages, always particularly cure the base coat around 50-75% of the recommended cure schedule to allow the top coat to properly cross-link with the base coat. This method of curing will result in the best possible bond between coats. over curing the base coat can cause possible Delamination between coatings. |