MIRROR ORANGE
EXCELLENT APPLICATION EFFICIENCY. THIS POWDER IS A SMOOTH FLOWING POLYESTER TGIC, WEATHER RESISTANT POWDER FOR INTERIOR OR EXTERIOR USE. OUTSTANDING RE-COATABILITY.
PC1115 |
MIRROR ORANGE |
CHEMISTRY |
POLYESTER TGIC A |
REGULAR CURE TEMP |
375F 13-20 MIN |
MIN TEMP |
356F 15-25 MIN |
MAX TEMP |
400F 10-15 MIN |
RECOMMENDED THICKNESS |
2.5-3.5 mils |
PENCIL HARDNESS |
2H minimum |
SPECIFIC GRAVITY |
1.2-1.8 g/cm3 |
THEORETICAL COVERAGE |
51.5 ft2 /lb at 2.5 mils |
PENCIL HARDNESS |
2H minimum |
GLOSS LEVEL (60°) |
80-95+ |
SALT SPRAY |
1,000 hours |
BALL IMPACT |
80 in/lb |
SDS Sheet info # |
#6A – Polyester TGIC (Group A) |
SDS link |
https://emeraldcoatings.com/sds-sheets/ |
WEATHER RESISTANT POWDER COATING FOR INTERIOR AND EXTERIOR APPLICATIONS, clear coat is not needed but will add extra protection. When coating in 2-3 stages, always particularly cure the base coat around 50-75% of the recommended cure schedule to allow the top coat to properly cross-link with the base coat. This method of curing will result in the best possible bond between coats. over curing the base coat can cause possible Delamination between coatings. |
MIRROR RED WILL BE OUT OF STOCK FOR FOR A LONG PERIOD OF TIME. CHECK OUT THESE CLOSE MATCHES THAT FLOW OUT JUST AS SMOOTH. RED BARON AND BLOOD RED
PC1116 |
MIRROR RED |
CHEMISTRY |
POLYESTER TGIC A |
REGULAR CURE SCHEDULE |
375F 13-20 MIN |
MIN RANGE |
356F 15-25 MIN |
MAX RANGE |
400F 10-15 MIN |
RECOMMENDED THICKNESS |
2.5-3.5 mils |
PENCIL HARDNESS |
2H minimum |
SPECIFIC GRAVITY |
1.2-1.8 g/cm3 |
THEORETICAL COVERAGE |
51.5 ft2 /lb at 2.5 mils |
PENCIL HARDNESS |
2H minimum |
GLOSS LEVEL (60°) |
80-95+ |
SALT SPRAY |
1,000 hours |
BALL IMPACT |
80 in/lb |
SDS Sheet info # |
#6A – Polyester TGIC (Group A) |
SDS link |
https://emeraldcoatings.com/sds-sheets/ |
WEATHER RESISTANT POWDER COATING FOR INTERIOR AND EXTERIOR APPLICATIONS, CLEAR COAT IS NOT NEEDED BUT WILL ADD EXTRA PROTECTION. When coating in 2-3 stages, always particularly cure the base coat around 50-75% of the recommended cure schedule to allow the top coat to properly cross-link with the base coat. This method of curing will result in the best possible bond between coats. over curing the base coat can cause possible Delamination between coatings. |
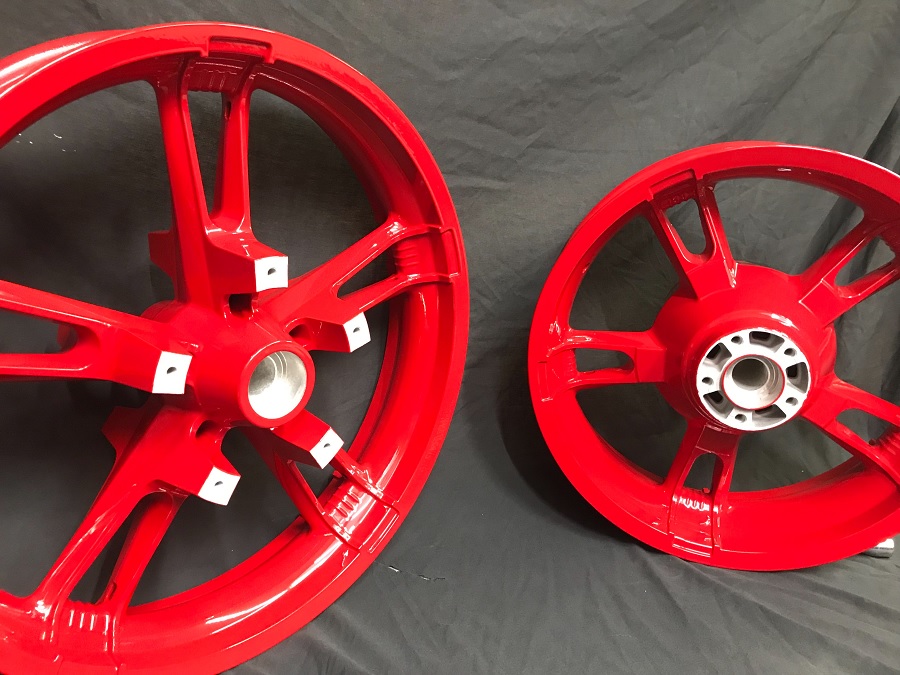
Description:Unsurpassed. No other word can adequately describe Cerakote C-7700 Glacier Silver coating. Formulated to withstand temperatures of over 2,000 degrees Fahrenheit and thermal shock from those temperatures directly into water with no adverse effects, C-7700 retains its bright silver, sleek satin finish in the most extreme environments. C-Series coatings are a line of air cured, ready to spray ceramic coatings.
Appearance
* Ultra smooth
* Bright silver, sleek satin finish
Application
* Easy to apply, Single coat, Air cure formula
* 70% solids yields higher coverage than normal high temperature coatings
* Exceptionally Bright Metallic Luster. Our brightest silver finish.
*Self-leveling properties
Performance
*Better thermal barrier properties than any other high temperature coating
* Industry leading heated and un-heated corrosion resistance
* No discoloration, even past 2000
*** SHAKE WELL BEFORE USE ***
***PLEASE STORE IN ROOM TEMP AND VENTILATE CONTAINER WEEKLY***
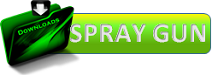
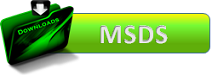
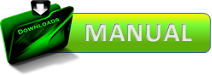
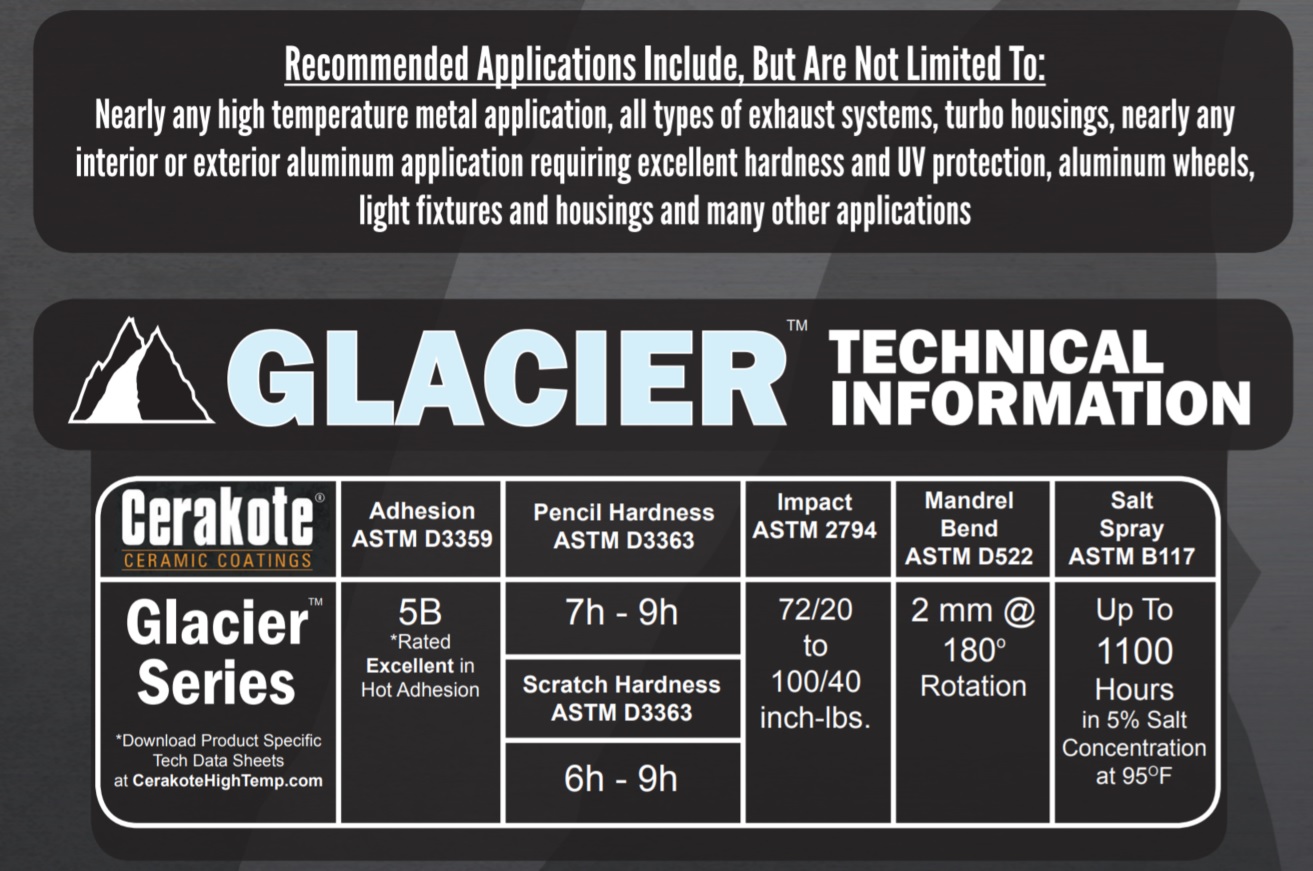
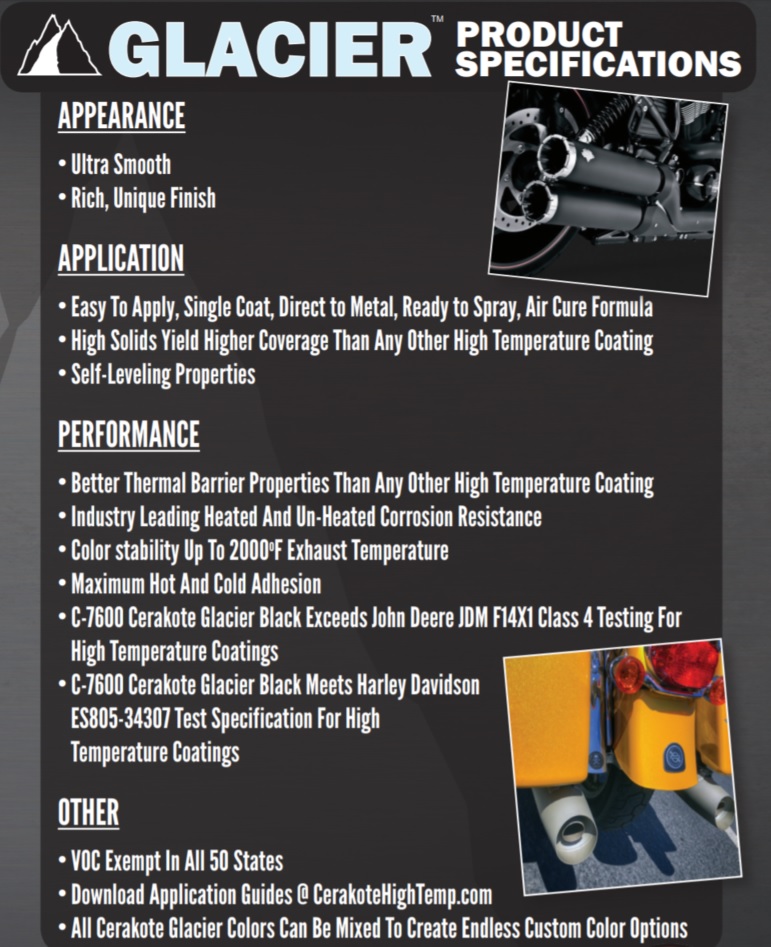
MIDNIGHT BLUE EXPLOSION ~ POLYESTER TGIC ~ DARK BLUE COLOUR THAT FLIPS AROUND WITH BRIGHT BLUE SPARKLES IN THE SUNLIGHT
CHEMISTRY |
MIDNIGHT BLUE EXPLOSION |
CHEMISTRY |
Polyester TGIC Metallic |
REGULAR CURE TEMP |
15 Minutes@ 375°F |
MIN TEMP |
NA |
MAX TEMP |
NA |
RECOMMENDED THICKNESS |
1.5 TO 3.5 MILS |
PENCIL HARDNESS |
2H |
SPECIFIC GRAVITY |
1.26 +/- .05 |
THEORETICAL COVERAGE |
56 sq/ft @ 2.0 mils |
PENCIL HARDNESS |
2H minimum |
GLOSS LEVEL (60°) |
85-95+ |
SALT SPRAY |
1,000 hours |
BALL IMPACT |
80 in/lb |
SDS Sheet info # |
#9 – Polyester TGIC Metallic |
SDS link |
https://emeraldcoatings.com/sds-sheets/ |
*Clear Coat Recommended, will Improved Mar Resistance and will improve the over all look and depth of the metallic finish. *When coating in 2-3 stages, always particularly cure the base coat around 50-75% of the recommended cure schedule to allow the top coat to properly cross-link with the base coat. This method of curing will result in the best possible bond between coats. Over curing the base coat can cause possible delamination between coatings. |
COMBINES ATTRACTIVE APPEARANCE WITH EXCELLENT MECHANICAL PROPERTIES.
PC1142 |
PENNY VEIN METALLIC |
CHEMISTRY |
POLYESTER TGIC B |
REGULAR CURE TEMP |
375F / 15 MIN |
MIN TEMP |
350F / 20 MIN |
MAX TEMP |
400F / 10 MIN |
RECOMMENDED THICKNESS |
2.0-3.0 mils |
PENCIL HARDNESS |
H minimum |
SPECIFIC GRAVITY |
1.40 +/-0.05 g/cm³ |
THEORETICAL COVERAGE |
137 sq.ft/lb/mil |
PENCIL HARDNESS |
2H minimum |
GLOSS LEVEL (60°) |
NA |
SALT SPRAY |
500 hours |
BALL IMPACT |
40 in/lb |
SDS Sheet info # |
#6B – Polyester TGIC (Group B) |
SDS link |
https://emeraldcoatings.com/sds-sheets/ |
*Clear Coat Recommended, will Improved Mar Resistance and will improve the over all look and depth of the metallic finish. *When coating in 2-3 stages, always particularly cure the base coat around 50-75% of the recommended cure schedule to allow the top coat to properly cross-link with the base coat. This method of curing will result in the best possible bond between coats. Over curing the base coat can cause possible delamination between coatings. |
ROCKSTAR BLACK TGIC POLYESTER POWDER
HAS A MIXTURE OF MEDIUM TO LARGE GOLD FLAKE THROUGH THE FINISH. GET THE MOST BLING FOR YOUR BUCK
CHEMISTRY |
ROCKSTAR BLACK |
CHEMISTRY |
Polyester TGIC Metallic |
REGULAR CURE TEMP |
375F 13-20 MIN |
MIN TEMP |
356F 15-25 MIN |
MAX TEMP |
400F 10-15 MIN |
RECOMMENDED THICKNESS |
1.5 TO 3.5 MILS |
PENCIL HARDNESS |
2H |
SPECIFIC GRAVITY |
1.26 +/- .05 |
THEORETICAL COVERAGE |
56 sq/ft @ 2.0 mils |
PENCIL HARDNESS |
2H minimum |
GLOSS LEVEL (60°) |
85-95+ |
SALT SPRAY |
1,000 hours |
BALL IMPACT |
80 in/lb |
SDS Sheet info # |
#9 – Polyester TGIC Metallic |
SDS link |
https://emeraldcoatings.com/sds-sheets/ |
*Clear Coat Recommended, will Improved Mar Resistance and will improve the over all look and depth of the metallic finish. *When coating in 2-3 stages, always particularly cure the base coat around 50-75% of the recommended cure schedule to allow the top coat to properly cross-link with the base coat. This method of curing will result in the best possible bond between coats. Over curing the base coat can cause possible delamination between coatings. |