SMOOTH FLOWING BLUE PEARLESCENT POWDER.
MC1023 |
COSMO BLUE |
CHEMISTRY |
Polyester TGIC Metallic |
REGULAR CURE TEMP |
400F/10 MIN @ PART METAL TEMPERATURE |
MIN TEMP |
NA |
MAX TEMP |
NA |
RECOMMENDED THICKNESS |
2.5-3.5 mils |
PENCIL HARDNESS |
2H minimum |
SPECIFIC GRAVITY |
1.2-1.8 g/cm3 |
THEORETICAL COVERAGE |
51.5 ft2 /lb at 2.5 mils |
PENCIL HARDNESS |
2H minimum |
GLOSS LEVEL (60°) |
80-95+ |
SALT SPRAY |
1,000 hours |
BALL IMPACT |
80 in/lb |
SDS Sheet info # |
#9 – Polyester TGIC Metallic |
SDS link |
https://emeraldcoatings.com/sds-sheets/ |
*Clear Coat Recommended, will Improved Mar Resistance and will improve the over all look and depth of the metallic finish. *When coating in 2-3 stages, always particularly cure the base coat around 50-75% of the recommended cure schedule to allow the top coat to properly cross-link with the base coat. This method of curing will result in the best possible bond between coats. Over curing the base coat can cause possible delamination between coatings. |
MIDNIGHT COPPER EXPLOSION ~ POLYESTER TGIC ~ DARK COPPER COLOUR THAT FLIPS AROUND WITH BRIGHT COPPER SPARKLES IN THE SUNLIGHT
• CURE TIME = 400F/10 MIN @ PMT (PART METAL TEMPERATURE) • RECOMMENDED MIL THICKNESS = 2.0 – 3.0 MILS • GLOSS LEVEL = 90+% • SPECIFIC GRAVITY = 1.34 • SALT SPRAY RESULTS = 1,000+ HOURS CLEAR COAT RECOMMENDED FOR EXTERIOR APPLICATIONS AND A BETTER GLASS LOOKING FINISH
MIDNIGHT TURQUOISE EXPLOSION POLYESTER TGIC POWDER
DARK TURQUOISE COLOUR THAT FLIPS AROUND WITH BRIGHT BLUE SPARKLES IN THE SUNLIGHT
CHEMISTRY |
MIDNIGHT TURQUOISE EXPLOSION |
CHEMISTRY |
Polyester TGIC Metallic |
REGULAR CURE TEMP |
15 Minutes@ 375°F |
MIN TEMP |
NA |
MAX TEMP |
NA |
RECOMMENDED THICKNESS |
1.5 TO 3.5 MILS |
PENCIL HARDNESS |
2H |
SPECIFIC GRAVITY |
1.26 +/- .05 |
THEORETICAL COVERAGE |
56 sq/ft @ 2.0 mils |
PENCIL HARDNESS |
2H minimum |
GLOSS LEVEL (60°) |
85-95+ |
SALT SPRAY |
1,000 hours |
BALL IMPACT |
80 in/lb |
SDS Sheet info # |
#9 – Polyester TGIC Metallic |
SDS link |
https://emeraldcoatings.com/sds-sheets/ |
*Clear Coat Recommended, will Improved Mar Resistance and will improve the over all look and depth of the metallic finish. *When coating in 2-3 stages, always particularly cure the base coat around 50-75% of the recommended cure schedule to allow the top coat to properly cross-link with the base coat. This method of curing will result in the best possible bond between coats. Over curing the base coat can cause possible delamination between coatings. |
FIRESIDE COPPER TOP COAT ~ POLYESTER TGIC ~ IN THE SHADE THIS PRODUCT IS A DEEP BROWN WITH HINTS OF COPPER, AS THE SUN SHINES IT BURNS WITH ALL THE INTENSITY OF THE SUN ITSELF. A BLACK BASECOAT ******BLACK BASECOAT RECOMMENDED
MC1029 |
FIRESIDE COPPER TOPCOAT |
CHEMISTRY |
Polyester TGIC Metallic |
REGULAR CURE TEMP |
15 Minutes@ 375°F |
MIN TEMP |
NA |
MAX TEMP |
NA |
RECOMMENDED THICKNESS |
1.5 TO 3.5 MILS |
PENCIL HARDNESS |
2H |
SPECIFIC GRAVITY |
1.2 +/- .05 |
THEORETICAL COVERAGE |
56 sq/ft @ 2.0 mils |
PENCIL HARDNESS |
2H minimum |
GLOSS LEVEL (60°) |
80-95+ |
SALT SPRAY |
1,000 hours |
BALL IMPACT |
80 in/lb |
SDS Sheet info # |
#9 – Polyester TGIC Metallic |
SDS link |
https://emeraldcoatings.com/sds-sheets/ |
WEATHER RESISTANT POWDER COATING FOR INTERIOR AND EXTERIOR APPLICATIONS. When coating in 2-3 stages, always particularly cure the base coat around 50-75% of the recommended cure schedule to allow the top coat to properly cross-link with the base coat. This method of curing will result in the best possible bond between coats. over curing the base coat can cause possible Delamination between coatings. |
PLUM PEARL
POLYESTER TGIC FREE POWDER
* 10 minutes at 375°F. @ P.M.T. * GLOSS @ 60 DEGREE METER-85+/-3% * RECOMMENDED MIL THICKNESS – 2.5-3.5MILS * SPECIFIC GRAVITY – 1.53 * SALT SPRAY RESULTS – 1,000 HOURS + COVERAGE- 126 sq. ft./lb/1 mi
*** CLEAR COAT NEEDED. EMERALD COATINGS RECOMMENDS A CLEAR FOR PROLONGED EXTERIOR USE AND IMPROVED MAR RESISTANCE.
ROCKSTAR WHITE
A TGIC POLYESTER POWDER THAT HAS A MIXTURE OF MEDIUM TO LARGE GOLD FLAKE THROUGH THE FINISH. GET THE MOST BLING FOR YOUR BUCK
CHEMISTRY |
ROCKSTAR WHITE |
CHEMISTRY |
Polyester TGIC Metallic |
REGULAR CURE TEMP |
375F 13-20 MIN |
MIN TEMP |
356F 15-25 MIN |
MAX TEMP |
400F 10-15 MIN |
RECOMMENDED THICKNESS |
1.5 TO 3.5 MILS |
PENCIL HARDNESS |
2H |
SPECIFIC GRAVITY |
1.83 +/- .05 |
THEORETICAL COVERAGE |
56 sq/ft @ 2.0 mils |
PENCIL HARDNESS |
2H minimum |
GLOSS LEVEL (60°) |
80-95+ |
SALT SPRAY |
1,000 hours |
BALL IMPACT |
80 in/lb |
SDS Sheet info # |
#9 – Polyester TGIC Metallic |
SDS link |
https://emeraldcoatings.com/sds-sheets/ |
*Clear Coat Recommended, will Improved Mar Resistance and will improve the over all look and depth of the metallic finish. *When coating in 2-3 stages, always particularly cure the base coat around 50-75% of the recommended cure schedule to allow the top coat to properly cross-link with the base coat. This method of curing will result in the best possible bond between coats. Over curing the base coat can cause possible delamination between coatings. |
ROCKSTAR YELLOW
A TGIC POLYESTER POWDER THAT HAS A MIXTURE OF MEDIUM TO LARGE GOLD FLAKE THROUGH THE FINISH. GET THE MOST BLING FOR YOUR BUCK
CHEMISTRY |
ROCKSTAR YELLOW |
CHEMISTRY |
Polyester TGIC Metallic |
REGULAR CURE TEMP |
375F 13-20 MIN |
MIN TEMP |
356F 15-25 MIN |
MAX TEMP |
400F 10-15 MIN |
RECOMMENDED THICKNESS |
2.5-3.5 mils |
PENCIL HARDNESS |
2H minimum |
SPECIFIC GRAVITY |
1.2-1.8 g/cm3 |
THEORETICAL COVERAGE |
51.5 ft2 /lb at 2.5 mils |
PENCIL HARDNESS |
2H minimum |
GLOSS LEVEL (60°) |
80-95+ |
SALT SPRAY |
1,000 hours |
BALL IMPACT |
80 in/lb |
SDS Sheet info # |
#9 – Polyester TGIC Metallic |
SDS link |
https://emeraldcoatings.com/sds-sheets/ |
*Clear Coat Recommended, will Improved Mar Resistance and will improve the over all look and depth of the metallic finish. *When coating in 2-3 stages, always particularly cure the base coat around 50-75% of the recommended cure schedule to allow the top coat to properly cross-link with the base coat. This method of curing will result in the best possible bond between coats. Over curing the base coat can cause possible delamination between coatings. |
ROCKSTAR RED . A TGIC POLYESTER POWDER THAT HAS A MIXTURE OF MEDIUM TO LARGE GOLD FLAKE THROUGH THE FINISH. GET THE MOST BLING FOR YOUR BUCK
CHEMISTRY |
ROCKSTAR RED |
CHEMISTRY |
Polyester TGIC Metallic |
REGULAR CURE TEMP |
375F 13-20 MIN |
MIN TEMP |
356F 15-25 MIN |
MAX TEMP |
400F 10-15 MIN |
RECOMMENDED THICKNESS |
2.5-3.5 mils |
PENCIL HARDNESS |
2H minimum |
SPECIFIC GRAVITY |
1.2-1.8 g/cm3 |
THEORETICAL COVERAGE |
51.5 ft2 /lb at 2.5 mils |
PENCIL HARDNESS |
2H minimum |
GLOSS LEVEL (60°) |
80-95+ |
SALT SPRAY |
1,000 hours |
BALL IMPACT |
80 in/lb |
SDS Sheet info # |
#9 – Polyester TGIC Metallic |
SDS link |
https://emeraldcoatings.com/sds-sheets/ |
*Clear Coat Recommended, will Improved Mar Resistance and will improve the over all look and depth of the metallic finish. *When coating in 2-3 stages, always particularly cure the base coat around 50-75% of the recommended cure schedule to allow the top coat to properly cross-link with the base coat. This method of curing will result in the best possible bond between coats. Over curing the base coat can cause possible delamination between coatings. |
ROCKSTAR ORANGE TGIC POLYESTER POWDER
HAS A MIXTURE OF MEDIUM TO LARGE GOLD FLAKE THROUGH THE FINISH. GET THE MOST BLING FOR YOUR BUCK
CHEMISTRY |
ROCKSTAR ORANGE |
CHEMISTRY |
Polyester TGIC Metallic |
REGULAR CURE TEMP |
375F 13-20 MIN |
MIN TEMP |
356F 15-25 MIN |
MAX TEMP |
400F 10-15 MIN |
RECOMMENDED THICKNESS |
2.5-3.5 mils |
PENCIL HARDNESS |
2H minimum |
SPECIFIC GRAVITY |
1.2-1.8 g/cm3 |
THEORETICAL COVERAGE |
51.5 ft2 /lb at 2.5 mils |
PENCIL HARDNESS |
2H minimum |
GLOSS LEVEL (60°) |
80-95+ |
SALT SPRAY |
1,000 hours |
BALL IMPACT |
80 in/lb |
SDS Sheet info # |
#9 – Polyester TGIC Metallic |
SDS link |
https://emeraldcoatings.com/sds-sheets/ |
*Clear Coat Recommended, will Improved Mar Resistance and will improve the over all look and depth of the metallic finish. *When coating in 2-3 stages, always particularly cure the base coat around 50-75% of the recommended cure schedule to allow the top coat to properly cross-link with the base coat. This method of curing will result in the best possible bond between coats. Over curing the base coat can cause possible delamination between coatings. |
ROCKSTAR BLUE . A TGIC POLYESTER POWDER THAT HAS A MIXTURE OF MEDIUM TO LARGE GOLD FLAKE THROUGH THE FINISH. GET THE MOST BLING FOR YOUR BUCK
CHEMISTRY |
ROCKSTAR BLUE |
CHEMISTRY |
Polyester TGIC Metallic |
REGULAR CURE TEMP |
375F 13-20 MIN |
MIN TEMP |
356F 15-25 MIN |
MAX TEMP |
400F 10-15 MIN |
RECOMMENDED THICKNESS |
2.5-3.5 mils |
PENCIL HARDNESS |
2H minimum |
SPECIFIC GRAVITY |
1.2-1.8 g/cm3 |
THEORETICAL COVERAGE |
51.5 ft2 /lb at 2.5 mils |
PENCIL HARDNESS |
2H minimum |
GLOSS LEVEL (60°) |
80-95+ |
SALT SPRAY |
1,000 hours |
BALL IMPACT |
80 in/lb |
SDS Sheet info # |
#9 – Polyester TGIC Metallic |
SDS link |
https://emeraldcoatings.com/sds-sheets/ |
*Clear Coat Recommended, will Improved Mar Resistance and will improve the over all look and depth of the metallic finish. *When coating in 2-3 stages, always particularly cure the base coat around 50-75% of the recommended cure schedule to allow the top coat to properly cross-link with the base coat. This method of curing will result in the best possible bond between coats. Over curing the base coat can cause possible delamination between coatings. |
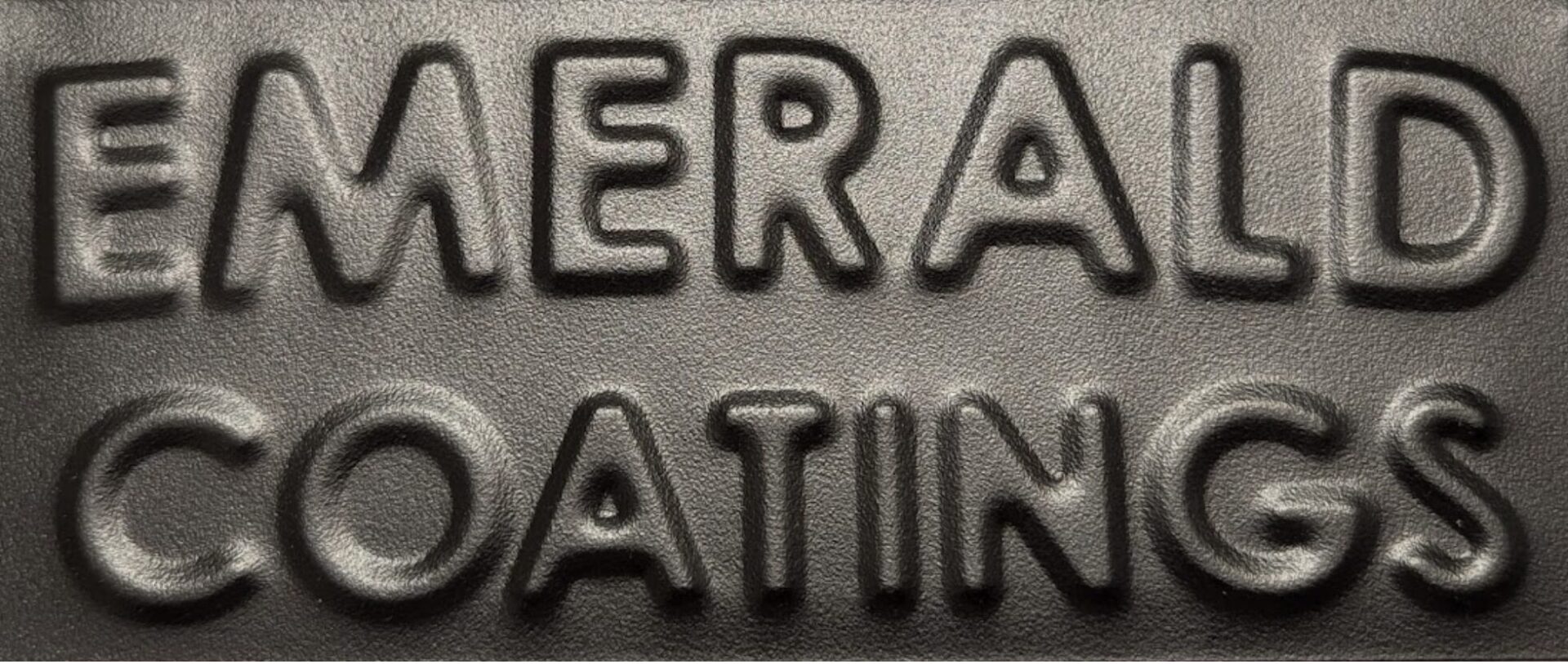
This is a black color with a textured finish. It’s a bit more grainy than our Black Carbide and Deep Flat Black Texture finishes, giving it a slightly rough surface. The finish has a matte look that is not shiny, providing a clean, industrial appearance. The texture is even and smooth to the touch, offering a durable and tough finish. This coating is perfect for surfaces that need to withstand wear and tear while maintaining a neat and professional look. It’s also easy to apply and work with, making it a fan favorite for automotive parts and laser-cut signs.
Recommended Colors With Similar Finishes
If you’re looking for other textured finishes, check out these options:
PC1021 |
BLACK TEXTURE 7-13% GLOSS |
CHEMISTRY |
POLYESTER TGIC C |
REGULAR CURE TEMP |
375F/15 min |
MIN TEMP |
NA |
MAX TEMP |
NA |
RECOMMENDED THICKNESS |
1.50 – 3.50 MILS |
PENCIL HARDNESS |
2H |
SPECIFIC GRAVITY |
1.69± 0.03 |
THEORETICAL COVERAGE |
NA |
PENCIL HARDNESS |
2H minimum |
GLOSS LEVEL (60°) |
NA |
SALT SPRAY |
1,000 hours |
BALL IMPACT |
80 in/lb |
SDS Sheet info # |
#6C – Polyester TGIC (Group C) |
SDS link |
https://emeraldcoatings.com/sds-sheets/ |
WEATHER RESISTANT POWDER COATING FOR INTERIOR AND EXTERIOR APPLICATIONS. USE ZINC RICH PRIMER OVER STEEL PARTS FOR EXTERIOR APPLICATIONS |
LAYS DOWN SUPER SMOOTH LICK GLASS. EXCELLENT BRIGHT RED. VERY CLOSE MATCH TO MIRROR RED. BLOOD RED IS A SLIGHT DARKER IN COLOUR.
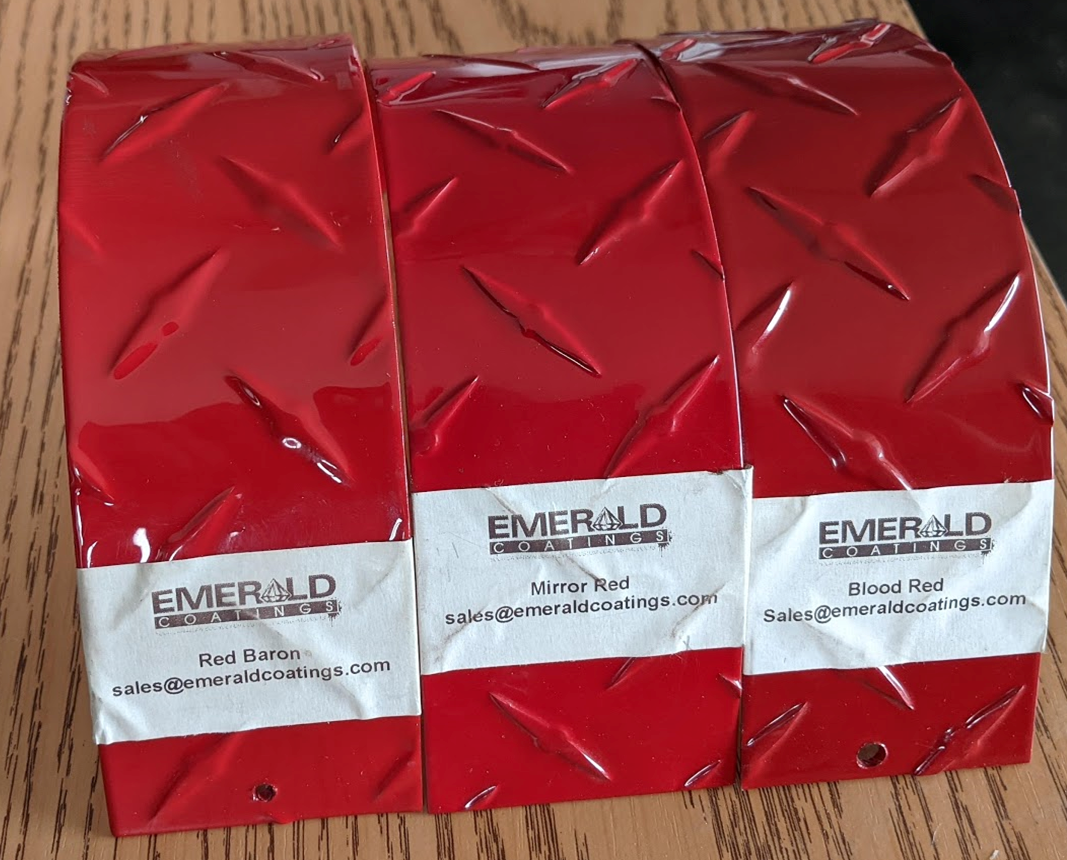
PC1023 |
BLOOD RED |
CHEMISTRY |
POLYURETHANE GROUP A |
REGULAR CURE TEMP |
375F/15 min |
MIN TEMP |
NA |
MAX TEMP |
NA |
RECOMMENDED THICKNESS |
1.9-2.2 mils |
PENCIL HARDNESS |
2H |
SPECIFIC GRAVITY |
1.3 +/-0.05 g/cm³ |
THEORETICAL COVERAGE |
147.92 sq.ft/lb/mil |
PENCIL HARDNESS |
2H minimum |
GLOSS LEVEL (60°) |
85+ |
SALT SPRAY |
2500 |
BALL IMPACT |
160 |
SDS Sheet info # |
#5A – Polyurethanes (Group A) |
SDS link |
https://emeraldcoatings.com/sds-sheets/ |
WEATHER RESISTANT POWDER COATING FOR INTERIOR AND EXTERIOR APPLICATIONS. A clear coat is recommended for outdoor applications. When coating in 2-3 stages, always particularly cure the base coat around 50-75% of the recommended cure schedule to allow the top coat to properly cross-link with the base coat. This method of curing will result in the best possible bond between coats. over curing the base coat can cause possible Delamination between coatings. |